Stepper motors are popular in computer and microcontroller-based position control applications like robotics, industrial automation, CNC machines, 3D printers and video camera control. Due to their uncomplicated internal construction and their limited number of connection wires, stepper motors look deceptively simple. On the internet, there are even lots of tutorials on how to control these motors using an antique L293D driver IC and an Arduino, but for serious applications everything depends on the quality and the capabilities of the motor driver.
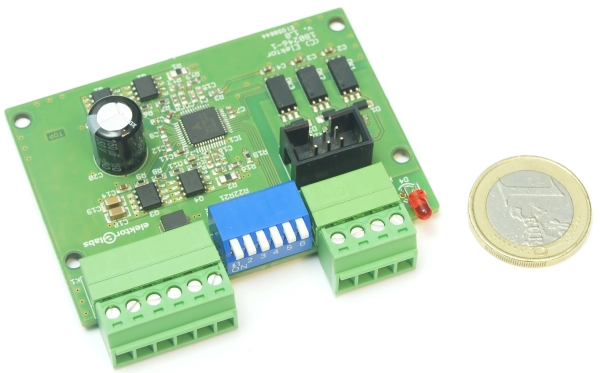
Commonly used stepper motor driver types
Stepstick drivers
If you are into hobby projects involving stepper motors or if you are building 3D printers, you are probably familiar with stepstick drivers. They consist of a small PCB with a stepper motor driver IC and pinheader connectors allowing the module to be plugged into a larger board.
Stepsticks come in many flavours allowing you to choose from a range of driver ICs from several semiconductor manufacturers. Some of the better stepsticks are the so-called SilentStepSticks built around Trinamic stepper driver ICs of which the TMC2100 and TMC2130 are the most popular ones.
These SilentStepSticks are a good choice for 3D printing applications, especially during lenghty print jobs. When using less advanced drivers, stepper motor noise may become objectionable soon. SilentStepSticks not only allow the printer to run silently but also help to achieve better, smoother and more consistent print results.
Besides the standard Enable, Step and Dir signals used to control the motor position, speed and direction, the TMC2130 and TMC5160 based stepsticks also have an SPI interface that allows tuning and configuring several driver parameters. Modern 3D printing software like Marlin supports these drivers and can even autotune the motor drivers via the SPI interface during printing for best results.
While stepsticks are small and easily swappable, they also have a number of disadvantages. Due to their very small size, most use driver ICs with integrated MOSFET bridges that tend to overheat on small boards with almost no copper planes, even with a heatsink mounted on top. This is mainly a problem in more demanding applications like CNC.
Furthermore, stepsticks don’t offer electrical isolation between the motor power supply and the control signals, making them less suitable for complex motion control systems.
Read more: FREE ELEKTOR ARTICLE: TMC2160 MOTOR DRIVER BOARD