Chapter 1: Introduction
1.1. Nails, Nail making and nail making machine
1.1.1 Nails
Nails, slender pin-shaped objects crafted from hard metal or alloy, serve as fasteners in various applications. Typically composed of steel, they are often treated with coatings to resist corrosion in harsh environments or enhance adhesion, thereby improving both functionality and appearance. Nails designated for woodwork are typically fashioned from soft, low carbon or mild steel, while those designed for concrete applications are constructed from harder materials.
Installation of nails is accomplished using tools such as hammers, nail guns, or explosive charges, securing materials together through axial friction and shear strength. With applications spanning from building and construction to carpentry, nails serve a multitude of purposes across industries. As a result, the varieties of nails available are extensive and diverse.
1.1.2 Nail Making
To achieve the desired diameter, wire is pulled through a sequence of dies. The wire end is then held and pressed into a die with the shape of the nail head, forming a knurled head for convenient striking when driving it into the workpiece for fastening.
Following this step, based on the desired nail length, the wire is cut using a die shaped to create the sharp point. The finished nail at this stage is transferred to a collection tray, awaiting the subsequent coating process.
1.1.3 Nail Making Machine
A nail making machine carries out several key operations, including head forming, wire cutting, and wire feeding.
During head forming, the nail head punch, knurled at its tip, is utilized. Its motion is derived from the motor-driven crankshaft. The design of the head punch must prioritize strength to effectively strike the wire without causing surface abrasions and withstand high impact loads. Additionally, it should possess sufficient hardness to prevent chipping of the striking surface.
In wire cutting, the cutting dies are shaped to achieve the pointed ends of the nails. They must be robust and harder than the nail wire to endure shearing forces that shape the pointed end. The cutting dies are timed to coordinate with the nail head punch.
Wire feeding involves the cam-driven pushing of the wire into the die block. The cam’s motion is derived from the support of the nail head punch or directly from the crankshaft. Timing is crucial in this operation to ensure the correct length of the nail is achieved at the appropriate moment.
1.2 Problem statement
Nail making machines are priced between Kshs 600,000 and 5,000,000, inclusive of taxes, resulting in the following issues:
i. Exclusion of potential participants from the cottage industry.
ii. Elevated expenses for imported nails.
iii. Importation of nail making machines at considerable costs.
The creation and implementation of a locally manufactured nail making machine will address these challenges. Furthermore, it will contribute to the realization of the industrialization goals outlined in Vision 2030.
1.3 Study Objective
The goal of this project is to create a nail making machine tailored to the needs of the local cottage industry. The specific objectives are as follows:
i) Conduct a survey of nail making machines presently employed in the local cottage industry.
ii) Develop a cost-effective nail making machine suitable for cottage industry operations.
iii) Generate a computer simulation model for the designed nail making machine.
iv) Assess the technical and economic feasibility of the innovative solution.
Chapter 2: Literature Review
2.1 Definition
A nail typically comprises a metal rod or shank, sharpened at one end and featuring a formed head at the opposite end, allowing it to be driven into wood or other materials for fastening purposes. Steel serves as the primary material in nail manufacturing, though aluminum, brass, and other metals are also viable options. Surface coatings or plating may be applied to enhance corrosion resistance, gripping strength, or aesthetic appeal. The head, shank, and point may assume various shapes depending on the nail’s intended function.
2.2 Background
Prior to the 19th century, nails were handcrafted by blacksmiths. Iron wire was positioned on an anvil, and one end was gradually tapered with the flat side of a hammer, forming a sharp edge about an inch from the end to create the nail’s pointed tip. Using the sharp end of the hammer, a notch was cut into the rod, after which the sharpened end was thrust into a tapered hole in the anvil and snapped off to produce the short nail. Subsequently, the nail’s end was flattened with rapid strikes of the hammer, and it was removed from the anvil hole with a quick, upward motion. This process illustrates the origins of nail making.
Nails may have been utilized in Mesopotamia as early as 3500 B.C., likely crafted from copper or bronze, before transitioning to iron. Initially, nails were hand-forged with hammers, manufactured individually, and thus were relatively scarce and costly.
By the 1500s, a machine was developed to produce long, flattened strips of iron known as nail rods, which could then be cut, pointed, and headed.
In the late 18th century, two early nail-making machines were patented, one by Ezekial Reed in the United States in 1786 and another by Thomas Clifford in England in 1790. These machines cut tapered pieces from flat iron sheets and subsequently flattened the heads. Despite these advancements, blacksmiths in rural areas continued handcrafting nails from wrought iron well into the 20th century.
The introduction of the first machine to produce nails from metal wire in the United States around 1850 marked a significant development, and this technique remains the primary method used in nail production today.
2.3 Applications of nails
Nails are commonly employed to join pieces of wood or fasten materials to wood. They are typically hammered into place and secured by friction, with some featuring roughened shanks to enhance grip. In residential housing construction, nails are extensively utilized, with an average wood frame house requiring anywhere from 20,000 to 30,000 nails of various types and sizes.
Given their diverse applications, nails come in a wide range of varieties. Common nails are the standard all-purpose option, while finishing nails, used in furniture and cabinetry, boast small heads that remain inconspicuous in the finished work. Nails are available in various lengths and gauges, or diameters.
Many nails feature notches or grooves near the head to improve grip, while some boast screw-like threads for added holding power. Specially hardened nails, engineered for use in concrete or masonry, feature longitudinally grooved shanks for a secure hold. Additionally, special double-headed nails are designed for temporary structure assembly.
2.4 Classification of nails
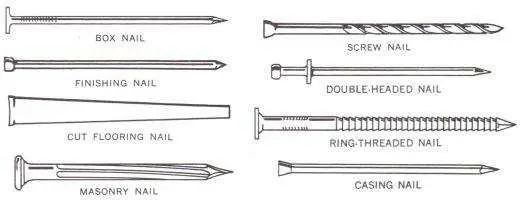
Although not precisely defined, nails are generally categorized based on their length. Typically, nails measuring less than 1 inch (2.54 cm) in length are referred to as tacks or brads. Nails ranging from 1 to 4 inches (2.54 to 10.16 cm) are simply called nails, while those exceeding 4 inches (10.16 cm) in length are sometimes termed spikes.
Box nails resemble common nails in their wire composition, but they feature thinner shanks and are not suitable for dimensional lumber framing construction, which typically requires common nails. This is because box nails have thinner shanks relative to their penny size, resulting in reduced holding power. They are commonly used on thinner wood materials, such as wooden boxes, to minimize splitting.
Upholstery nails serve as decorative elements for furniture, providing a final touch to various furniture types.
2.5 Design
The shank of a nail is typically crafted to be round and smooth. However, shanks featuring serrations, annular grooves, spiral flutes, or helical threads are utilized when a stronger and more permanent grip is necessary. Additionally, thermoplastic coatings may be applied to the shaft, which heat up due to friction during nail driving, then rapidly cool and set to secure the nail in place. The diameter of the shank varies depending on the nail type.
The most common nail point is a four-sided tapered cut known as a diamond point. However, other nails may feature a blunter point to prevent certain woods from splitting. Specialized nails may also include chisel points, barbed points, needle points, and various others, tailored to specific applications.
Various types of nails are available for different purposes, including tile roofing, hardwood flooring, shingles, rain gutters, wallboard, sheet metal, and concrete. Some nails are specifically designed to be driven using air-powered nail guns rather than a hammer. Moreover, there have been advancements in nail design tailored for specific applications within the aerospace industry.
2.6 Raw Materials
The majority of nails are constructed from steel, although alternative materials such as aluminum, copper, brass, bronze, stainless steel, nickel silver, monel, zinc, and iron are also employed. Galvanized nails undergo a zinc coating process to enhance their resistance to corrosion. Blued steel nails are exposed to flames to acquire a bluish oxide finish, offering a degree of corrosion resistance. Cement-coated nails are coated with a plastic resin to enhance their gripping capabilities. Certain brads receive a colored enamel coating to harmonize with the color of the material they are securing.
2.7 The Manufacturing process
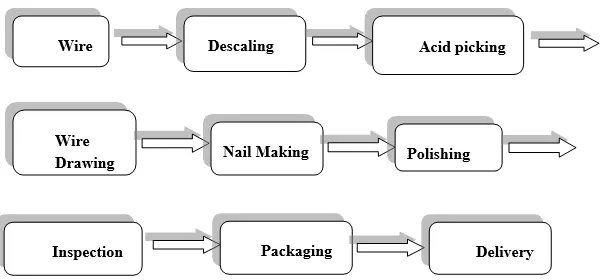
Wire is extracted from a coil and introduced into the nail-making apparatus, where it is grasped by a pair of gripping dies. The head shape of the nail has been precisely crafted into the ends of these dies. As the dies secure the wire in place, a mechanical hammer strikes the free end of the wire, causing it to deform into the die cavity, thereby shaping the head of the nail. While the wire remains clamped in the dies, a set of shaped cutters impacts the opposite end of the nail, simultaneously forming the point and severing the nail from the remaining wire extending from the coil. Subsequently, the dies open, and an expelling mechanism propels the nail into a collection pan situated beneath the machine. The free end of the wire is then drawn from the coil and fed back into the machine, initiating the cycle once more.
2.8 The Future
The demand for mass-produced commodity nails is influenced by fluctuations in the construction industry, which are closely tied to economic conditions. Additionally, competition from foreign manufacturers poses a challenge, further squeezing profits.
In Kenya, the adoption of nail production has been hindered by the unaffordability of nail making machines. However, with population and economic growth driving increased demand for housing, the need for nails is on the rise. Similar to other markets, competition from foreign manufacturers remains a factor, impacting profit margins.
Key desirable attributes of a nail making machine include smooth operation, minimal wear and tear, low maintenance costs, high durability, and superior efficiency.
CHAPTER 3: Methodology
The aim of this project was to create an economical and accessible nail making machine tailored for the cottage industry in Kenya. With its completion, our aspiration is for this machine design to be widely adopted across the cottage industry in Kenya. Additionally, by manufacturing the nail making machine domestically, we anticipate a significant reduction in its cost, thereby fostering job creation within the sector and contributing to the objectives outlined in Vision 2030.
Initially, we conducted site visits to several nail industries in Kenya, such as Wire Products in Athi River and Devki Steels in Ruiru, where we observed that the existing machines were primarily imported from India. Additionally, we collected literature on existing machine designs from various countries known for nail manufacturing, including China, the USA, and India.
Utilizing this information, we developed design matrices to identify the key attributes of a reliable nail making machine and determine which features and mechanisms could be modified to create an affordable solution. Subsequently, we generated CAD drawings using Autodesk Inventor.
The objectives of this project will be realized through subsequent stages, which include analyzing existing nail making machine designs to identify those suitable for fabrication using locally available materials and machinery, creating a computer simulation using Autodesk Inventor, and assessing the overall quality of the nail making machine, particularly in terms of production costs.
3.1. A Survey of Nail Making Machines Currently Being Used In the Cottage Industry
In the current technological landscape, numerous nail making machine designs cater to the needs of the manufacturing and construction industries. These machines are manufactured abroad by various companies across countries such as India, China, and the USA. Each machine is tailored to produce specific nail designs, such as box nails, screw nails, finishing nails, and cut flooring nails, with variations to accommodate different nail lengths.
Our primary emphasis was on compact and efficient nail making machines. Our secondary objective involved selecting a machine design that aligns closely with the requirements of the Kenyan building and manufacturing sectors while remaining cost-effective.
3.1.1. Current Nail Making Machine Designs
The initial step in evaluating nail making machine designs involved researching the existing products available in the industry. Upon inquiry, we discovered that there were only a few nail manufacturers operating locally. Devki Steels in Ruiru and Wire Products in Athi River emerged as the primary manufacturers of nails in the area.
To commence our research, we visited Devki Steels Ltd to inspect their machinery. During our visit, we met with the maintenance engineer, who provided us with insights into the company’s history of nail production, primarily importing machines from India. He demonstrated the nail making process and showcased the range of nails they manufactured. Notably, we learned that the company did not produce roof nails due to the exorbitant costs associated with the machines, which were priced at approximately US $8,000. Factoring in shipping expenses and taxes, the total cost would exceed US $10,000.
According to the engineer, the high costs deterred many companies from investing in the machines, resulting in limited local production and consequently higher nail prices. This created unfair competition with cheaper imported nails, reducing the demand for locally manufactured products. Subsequently, we conducted online research to explore nail making machines predominantly imported from India, China, and the USA, leading us to identify the following designs.
3.1.2. Perfect Automatic Wire Nail making machine
This model is produced in Punjab, India.
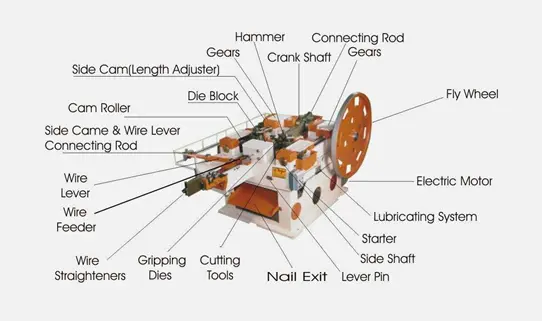
It boasts a simple yet robust design, crafted from premium-grade casting and steel materials. With a versatile range, it can produce various types of nails including flat head, pop, round head, lost head, and counter sunk head nails from copper, aluminum, and brass wires.
Its primary crank is directly powered by a motor, while side-shafts are driven by four bevel gears, ensuring precise and consistent adjustment of the cutting tool. The machine allows for adjustable nail length and thickness, with all tools easily accessible and replaceable for swift maintenance. Equipped with bushes on its main and side shafts, it guarantees extended durability.
Constructed with high-quality steel components, including cams, gears, rollers, and roller pins, properly heat-treated and ground, the machine ensures long-lasting performance.
The wire from the coil passes through straightening rollers and is intermittently fed into the gripping dies, which securely close to allow the heading punch to shape the nail head. Subsequently, the grip loosens, and the required nail length is continuously fed, cut by the cutting tools, leaving sufficient stock for the head of the subsequent nail. The finished nail is then ejected by the ejector.
The machine is priced at Kshs. 166,000, excluding shipping costs, which could amount to over Kshs. 300,000.
3.1.3. Nail making machine – USA
This innovation originates from the United States of America.

Similar to the previous model, this one also utilizes a main shaft and side cams as the primary power transmission system to the dies. However, it differs from the aforementioned model in several aspects that enable it to operate at a higher speed.
The distinguishing features of this machine lie in its method of driving the reciprocating heading ram using a balanced flywheel and crank construction. This construction allows the crankshaft to operate at a higher speed in perfect balance, despite the rapidity with which the ram forms the nail heads. Additionally, the machine incorporates a continuously rotating ejector mechanism to efficiently clear the cut nails from the machine, with the ejector operating in precise timed relation with the heading ram.
Furthermore, the machine includes a mechanism for operating the wire grippers using preloaded torsion members, ensuring firm wire grip during the heading operation. These torsion members are designed to unload the gripping members only when the wire is being fed after the heading operation.
These distinguishing features set this machine apart from the one originating from Punjab, India.
Follow this link for complete project: DESIGN OF A NAIL MAKING MACHINE SUITABLE FOR THE LOCAL COTTAGE INDUSTRY